Book Downloads Hub Reads Ebooks Online eBook Librarys Digital Books Store Download Book Pdfs Bookworm Downloads Book Library Help Epub Book Collection Pdf Book Vault Read and Download Books Open Source Book Library Best Book Downloads Edgar Fahs Smith Paula Findlen Vijay Govindarajan Negar Mottahedeh Kezia Noble Scott Payne Sairam Bhat Herman Melville
Do you want to contribute by writing guest posts on this blog?
Please contact us and send us a resume of previous articles that you have written.
Revolutionizing Manufacturing and Services Industries: The Power of SPC and TQM

In today's highly competitive business landscape, maintaining superior quality standards has become the cornerstone of success for manufacturing and services industries. Companies that consistently deliver exceptional products and services while minimizing defects and waste gain a significant competitive advantage. This is exactly where Statistical Process Control (SPC) and Total Quality Management (TQM) steps in.
Whether you are a manufacturer striving for defect-free production or a service provider aiming for excellent customer satisfaction, implementing SPC and TQM methodologies can drive remarkable improvements in quality and overall business performance. Let's take a closer look at how these two methodologies revolutionize the manufacturing and services sectors.
Statistical Process Control (SPC): A Game-Changer for Manufacturers
Manufacturing processes involve various complex operations and numerous interdependent variables. Maintaining consistent quality throughout these processes can be a daunting task. However, with SPC, manufacturers can gain real-time control over their operations and continuously monitor and improve their processes.
5 out of 5
Language | : | English |
File size | : | 5561 KB |
Text-to-Speech | : | Enabled |
Screen Reader | : | Supported |
Enhanced typesetting | : | Enabled |
Word Wise | : | Enabled |
Print length | : | 154 pages |
SPC is a statistical technique that uses statistical analysis tools to measure and control process variations, subsequently ensuring consistent quality outcomes. By leveraging SPC, manufacturers can identify the root causes of process variations, make data-driven decisions, and implement preventive measures to avoid defects.
SPC involves the following key steps:
Data Collection: Gathering relevant data points and measurements at different stages of the manufacturing process.
Data Analysis: Statistical analysis of collected data to identify trends, patterns, and variations.
Control Charts: Construction of control charts, such as X-Bar and R-Chart, to monitor process variability and identify when intervention is required.
Process Improvement: Continuous improvement initiatives driven by SPC insights to minimize defects, reduce waste, and enhance overall process capability.
By implementing SPC, manufacturers can achieve the following benefits:
- Improved product quality, adhering to customer specifications.
- Reduced defects and waste, leading to cost savings.
- Enhanced process capability and productivity.
- Increased customer satisfaction and loyalty.
Total Quality Management (TQM): Revolutionizing Service Industries
TQM, on the other hand, focuses on delivering exceptional service quality consistently. In service industries where tangible products are not manufactured, the quality of customer experiences becomes paramount. TQM provides a comprehensive framework to address every aspect of service quality across all organizational levels.
TQM encompasses the following principles:
- Customer Focus: Understanding and satisfying customer needs, expectations, and preferences.
- Continuous Improvement: Continuously enhancing processes, products, and services to achieve optimal quality standards.
- Employee Involvement: Involving and empowering employees to contribute to quality improvement initiatives.
- Process Orientation: Focusing on efficient and effective process management to deliver consistent quality outcomes.
- Supplier Relationships: Collaborating with suppliers to maintain high-quality inputs and strengthen the overall supply chain.
By implementing TQM, service industries can achieve the following benefits:
- Higher customer satisfaction and loyalty through consistently exceptional service delivery.
- Improved employee morale and engagement by involving them in quality improvement initiatives.
- Streamlined processes and reduced variations, leading to increased operational efficiency.
- Enhanced organizational reputation and brand image.
Combining SPC and TQM: Unleashing the Power of Quality
In manufacturing and service industries, the integration of SPC and TQM can result in an unparalleled level of quality excellence. By combining the principles of SPC and TQM, organizations can establish a robust quality management system that covers every stage of their operations.
The key benefits of combining SPC and TQM include:
- Improved process control by identifying and addressing quality issues proactively.
- Early detection of process variations and aberrations, leading to timely corrective actions.
- Ongoing process optimization and performance improvement.
- Reduced product defects and service failures, resulting in higher customer satisfaction.
- Increased profitability through cost savings achieved by minimizing waste and rework.
Organizations that successfully implement SPC and TQM methodologies witness extraordinary improvements in their quality and customer satisfaction levels. Moreover, they gain a significant competitive edge in the marketplace, ultimately resulting in sustainable growth and profitability.
The manufacturing and services industries are continuously evolving, demanding organizations to embrace innovative approaches to quality management. SPC and TQM, when used in tandem, offer a powerful solution to achieve excellence in quality, customer satisfaction, and overall business performance.
By leveraging SPC's statistical techniques and TQM's comprehensive framework, organizations can identify and control process variations, continuously improve their operations, and deliver exceptional products and services. It's time for manufacturers and service providers to harness the power of SPC and TQM and embark on an exciting journey of quality revolution!
5 out of 5
Language | : | English |
File size | : | 5561 KB |
Text-to-Speech | : | Enabled |
Screen Reader | : | Supported |
Enhanced typesetting | : | Enabled |
Word Wise | : | Enabled |
Print length | : | 154 pages |
This book comprehensively explores all of the underlying issues and elements which, together, constitute one of the most successful quality and management programmes upon which companies such as Motorola and GE base their success - Six Sigma. The author was directly involved in implementing Six Sigma quality principles and practices into a European division of GE Capital, deploying this initiative in an entirely service-oriented business for the first time. Drawing from and reflecting on his experience, Geoff Tennant develops a reasoned exploration of the benefits that Six Sigma offers to any organization and what can be expected from start to finish. He investigates the relationship between Six Sigma and quality, customer satisfaction, business processes and organizational structure, statistics and analysis and process improvement methodologies. Aimed at quality professionals, senior management and directors, as well as practitioners and students of Six Sigma, Six Sigma: SPC and TQM in Manufacturing and Services provides an in-depth but highly readable insight into the quality initiative that is certain to sweep European companies as it has large and global American corporations.
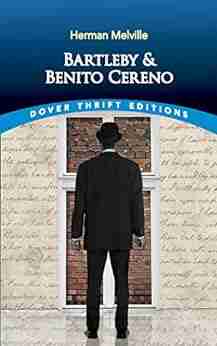

Unmasking the Enigma: A Colliding World of Bartleby and...
When it comes to classic literary works,...
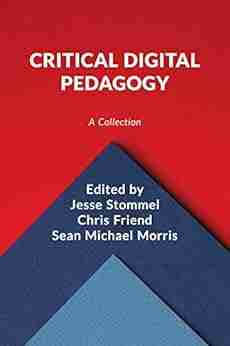

Critical Digital Pedagogy Collection: Revolutionizing...
In today's rapidly evolving digital...
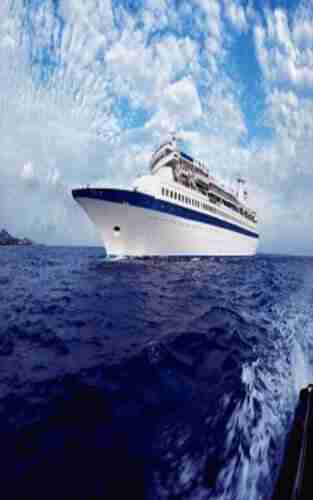

The Diary Of Cruise Ship Speaker: An Unforgettable...
Embark on an incredible...
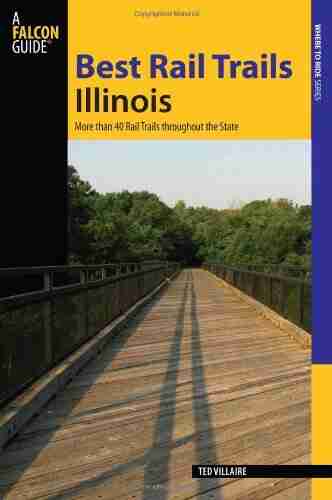

Best Rail Trails Illinois: Discover the Perfect Trails...
If you're an outdoor enthusiast looking...
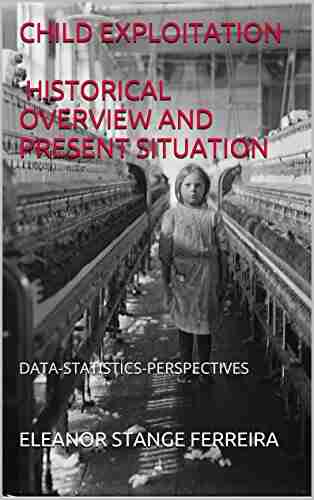

Child Exploitation: A Historical Overview And Present...
Child exploitation is a...
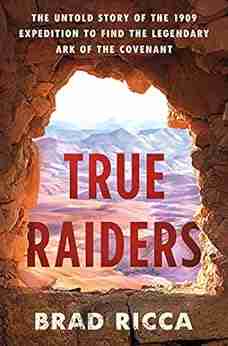

The Untold Story Of The 1909 Expedition To Find The...
Deep within the realms of legends and...
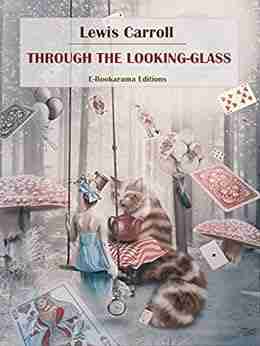

Through The Looking Glass - A Wonderland Adventure
Lewis Carroll,...
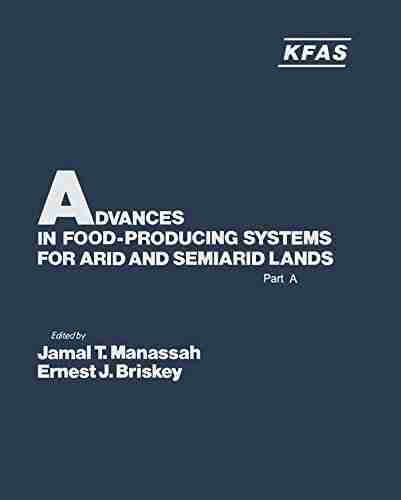

Advances In Food Producing Systems For Arid And Semiarid...
In the face of global warming and the...
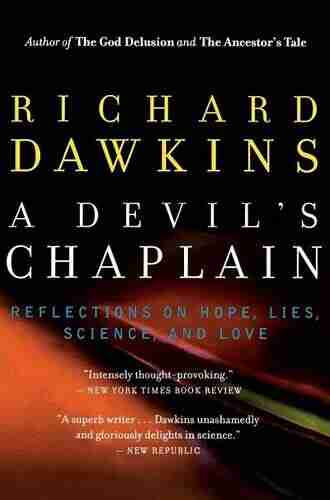

The Devil Chaplain: Exploring the Intriguing Duality of...
When it comes to the relationship between...
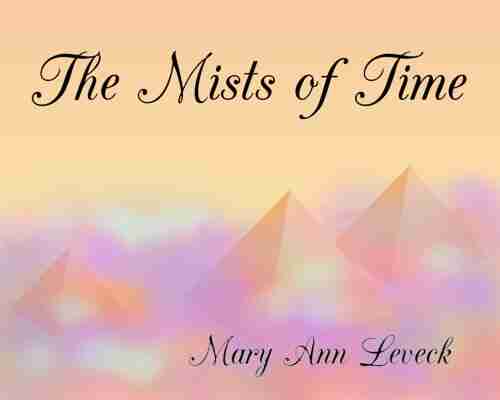

The Mists of Time: Cassie and Mekore - Unraveling the...
Have you ever wondered what lies beyond...
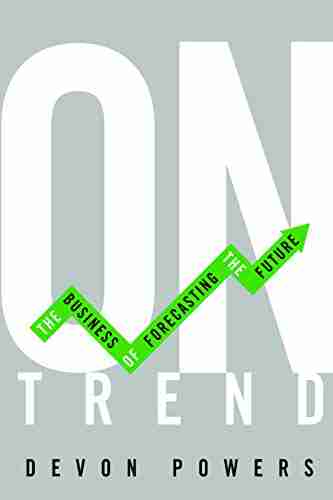

On Trend: The Business of Forecasting The Future
Do you ever wonder what the future holds?...
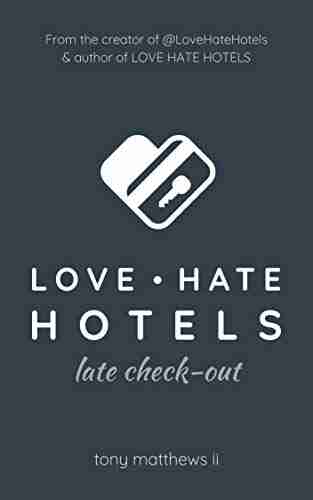

Love Hate Hotels Late Check Out
Have you ever experienced the joy of...
Light bulbAdvertise smarter! Our strategic ad space ensures maximum exposure. Reserve your spot today!
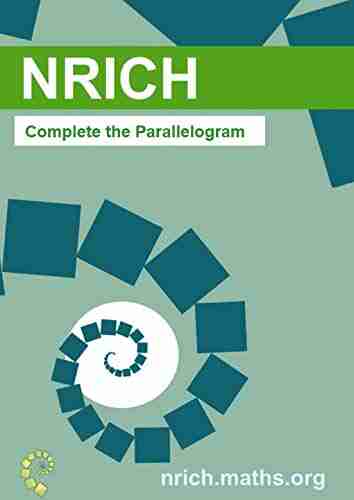

- Harold PowellFollow ·16.9k
- Jerome BlairFollow ·5.5k
- Henry HayesFollow ·5.7k
- Italo CalvinoFollow ·18.6k
- Joseph HellerFollow ·2.3k
- Barry BryantFollow ·16.7k
- Timothy WardFollow ·5.5k
- Ernest J. GainesFollow ·12.6k